石墨加工廠在進行石墨化時要如何改造供電設備?
石墨加工廠紛紛改造交流石墨化為直流石墨化,都獲得了不同的節電作用。到20世紀80年代末交流石墨化爐多數現已篩選,每噸石墨電極的能源消耗水平大約下降了30%左右(20世紀80年代末與70年代末比較)。但是石墨加工廠直流石墨化供電設備標準不一致,輸出直流電流及電壓調度規模與石墨化爐長度合作不盡合理,影響節電作用,一批容量較小的3.340~6.680MV·A直流供電設備有待于升級改造,直流送電的石墨化爐的節電還大有潛力可挖。石墨化爐通電時上升功率受溫升操控,變壓器功率輸出從低到高,到達最高功率后又逐漸下降,因此通電全過程的平均功率只有變壓器容許最大功率的50%左右。國內已有幾家炭素廠研討了恒功率通電的可能性,改動輸出電壓和電流等級,以便前進石墨化爐在通電過程中的平均功率,充分利用變壓器的供電才干,縮短通電時間,下降每噸石墨化品的電耗,業已獲得必定作用,為石墨化爐節電開辟了一條新路。
石墨化供電設備的改造。石墨化爐是“電老虎”。石墨化生產的節電一是從工藝上著手改進,如合理裝爐、使用適宜的電阻料、編制能充分發揮供電設備效能的送電曲線;二是改交流送電為直流送電。交流石墨化爐為單相用電,單相交流用電會構成電網相不平衡,并且交流石墨化爐短網的電感丟失大,功率因數低。跟著大功率整流設備的過關,石墨化爐選用直流送電的條件逐漸老到。國外最早使用直流送電是在20世紀60年代中期。吉林石墨加工廠在研討國內外石墨化節能技術的基礎上,于1975年自行設計、制作設備建成了第一組大功率直流石墨化供電機組,經運轉驗證完成了電網的三相平衡,前進了功率因數,并且由于起伏增大了經過爐芯的電流密度,不只升高了爐溫(從曩昔的 2300~2500℃左右前進到2500~2700℃),一起也縮短了送電時間,因此有利于前進優級品率,添加產量及下降電耗(每噸制品約下降100kWh)。到“七五”期末,吉林炭素廠的八組交流(變壓器容量為5000kV·A)石墨化爐合并改構成六組直流石墨化爐(變壓器容量增至16.000~20.000MV·A)。吉林石墨加工廠三組石墨化爐改造前后技術目標比照。
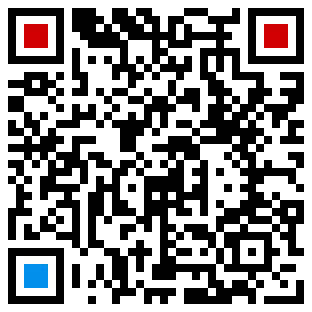
