石墨塊熱壓溫度是多少?
高取向石墨塊的高溫熱導率圖9顯示了由86wt%+32目鱗片石墨和14wt%AR瀝青制成的石墨樣品在不同溫度下的比熱容、熱擴散率和熱導率。從圖中可以看出,隨著試驗溫度的升高(25~1000℃),石墨塊的比熱容逐漸增大,最后趨于穩定;石墨塊的熱擴散系數和導熱系數隨著試驗溫度的升高而逐漸降低,最終趨于平緩。這是因為碳(石墨)材料的熱導率主要是由晶格原子的熱振動引起的。在一定溫度下,晶體中原子的熱振動有一定的振幅。石墨晶體受熱后,其晶格的熱振動加劇,振幅增大,聲子運動的阻力也增強。另外,溫度越高,聲子碰撞的幾率越大,平均自由程越短,對應的熱阻越大,即熱導率越低[5],所以材料的熱導率隨著測試溫度的升高而降低。與石墨材料的導熱系數相似,傳統金屬材料(如銅)的導熱系數隨著測試環境溫度的升高而明顯下降。雖然下降幅度不是很大,但是如果在空氣氣氛中或者有氧環境中溫度升高,金屬會明顯氧化形成一種導熱系數非常低的氧化物,所以金屬的應用領域和環境受到一定的限制。而石墨材料不存在。
解決了這個問題,在400℃以下的有氧環境下仍然可以使用,特別是在集成電路、封裝技術等微納電子領域。電子元器件的工作環境溫度一般在50~100℃以內,石墨材料在此溫度下具有較高的熱擴散率和熱導率(270~370 mm2/s和570 ~ 600 W/(m·k))。結合其低熱膨脹系數和良好的熱機械性能,通過工藝控制和結構設計,它可以是具有定向(面對面)導熱性(受到另一個方向上的低導熱性的限制,這可能不足以作為三維塊體導熱材料)的熱管理裝置。石墨材料這些獨特的熱特性決定了它有望在熱管理領域部分替代傳統金屬材料。
瀝青結合料的種類和用量瀝青結合料在制備石墨材料的過程中起著非常重要的作用。它能包覆鱗片石墨顆粒,將各種大塊顆粒粘結在一起,填充內部空隙,形成質地均勻、可塑性好的糊狀物,使粘結劑在高溫炭化過程中自身焦化形成內聚性焦炭,將大塊顆粒結合成一個堅固的整體,使材料制品具有所需的機械強度和其他性能。從圖1(b)可以看出,瀝青粘結劑涂覆或包裹在天然鱗片石墨表面,經過高溫碳化和石墨化后,形成瀝青焦和石墨膜/顆粒,覆蓋在天然鱗片石墨表面,形成大量石墨制品的表面/界面,對碳(石墨)制品的導熱性能有很大影響。不同種類(性質)的瀝青結合料形成的焦炭、碳和石墨具有不同的微晶結構和取向,其微晶尺寸和石墨化程度也不同,這將極大地影響石墨材料的導熱性能。
金屬摻雜處理據報道,添加一些催化顆粒(如Si、Ti、Zr等。)到碳(石墨)材料中可以顯著提高石墨材料的熱導率。特別是中國科學院山西煤炭化學研究所劉等人[2,10-11]以天然石墨、瀝青和摻雜劑(Si和Ti粉)為原料,在2700~3000℃的高溫下
在20~30 MPa下熱壓制備的摻雜石墨的熱導率在室溫下高達456 ~ 704 W/(m·k),明顯高于純石墨的熱導率(351 W/(m·k))。在這項研究中,硅和鈦金屬粒子分別用于摻雜碳塊。在相同的工藝條件下(+32目鱗片石墨,14wt% AR瀝青粘結劑,500℃熱壓,10 MPa壓力等。),摻雜石墨塊的物理性能如表6所示。從表中可以看出,摻雜得到的石墨制品的體積密度較低,這是由于摻雜后組分間熱膨脹系數不匹配(金屬的熱膨脹系數明顯高于石墨)以及高溫熱處理時形成的碳化物重新分解,導致石墨塊的體積密度降低。摻雜石墨塊的室溫電阻率明顯高于未摻雜的純石墨塊,其熱擴散率和熱導率明顯低于未摻雜的石墨塊。這與其體積密度的降低、內部石墨片層有序堆積結構的改變以及材料中摻雜顆粒引起的點缺陷或晶界增大引起聲子散射不利于聲子傳播有關[5]。
表1顯示了用+32目片狀石墨和14wt%不同瀝青粘合劑制備的碳塊樣品在2800℃石墨化后的物理性能。從表中可以看出,以WISCO瀝青WG和萘瀝青NP為粘結劑制備的石墨塊的堆密度較低,這與瀝青的軟化點、殘炭率較低,揮發分含量較高有關(表2)。這兩種石墨塊具有較高的室溫電阻率、較低的熱擴散率和熱導率,這不僅與它們較低的堆積密度有關,還與WG瀝青較高的灰分含量有關。用萘基中間相瀝青MP和AR作為粘結劑制備的石墨塊的堆積密度較高,這與瀝青的軟化點、焦炭產率較高和揮發物含量較低有關(表2)。所制備的石墨塊具有較低的室溫電阻率、較高的熱擴散率和熱導率,這與其較高的堆積密度和較低的瀝青灰分含量密切相關。MP瀝青制成的石墨塊電阻率最低,為1.27ω·m,室溫下的熱擴散率和熱導率高達386 mm2/s和530 w/(m·k),略低于AR瀝青為粘結劑制成的石墨塊。這可能與中間相瀝青的灰分含量、光學結構和熱流動性有關。以東道碳SC瀝青為粘結劑制備的石墨塊堆積密度不高,高溫石墨化后沿石墨塊厚度方向略有膨脹,這可能與瀝青粘結劑的各向同性結構和性能有關。然而,所獲得的石墨塊在室溫下的電阻率低,并且在室溫下的熱擴散率和熱導率也高。這說明以高軟化點、高殘炭率的瀝青為粘結劑制備的石墨塊具有良好的導電性。這些瀝青原料在2800℃石墨化得到的石墨顆粒的微晶尺寸(Lc,La)和石墨化度(G)是不同的(表3)。WG瀝青基石墨最小,SC瀝青基石墨次之,AR瀝青基石墨最大。源自瀝青的石墨顆粒的不同尺寸的微晶可能具有不同程度的完整性和在石墨塊中形成的連接傳導通道的優選取向,這將對石墨材料的熱傳導產生不同的影響。瀝青衍生石墨的微晶尺寸越小,石墨塊的熱導率越低。石墨微晶尺寸越大,石墨塊的導熱系數越高。
不同瀝青在2800℃石墨化得到的石墨顆粒的偏光顯微照片如圖5所示。從圖中可以看出,WG瀝青基石墨顆粒具有細小的鑲嵌結構,石墨微晶尺寸較小,因此其取向性較差。因此,以WG瀝青為粘結劑制備的石墨塊導熱系數較低。NP基石墨顆粒具有粗大的鑲嵌結構,部分區域具有明顯的取向結構,石墨微晶的尺寸和取向明顯提高,這可能與瀝青聚合形成流線型結構大分子有關,因此以其為粘結劑制備的石墨塊的導熱系數也有所提高。鈧基石墨顆粒主要是粗鑲嵌結構。雖然石墨微晶的尺寸比WG瀝青大,但晶體的取向度不是很高,所以以SC基石墨顆粒為粘結劑制備的石墨塊的導熱系數不是很高。MP基石墨顆粒具有明顯的長程微晶堆積和擇優取向結構,晶粒尺寸較大。瀝青在熔化和流動過程中形成的石墨片層取向度較高,有利于制備高導熱石墨材料。特別是熱處理過程中的AR瀝青
形成的石墨顆粒具有明顯的碳層堆積和長程有序結構,石墨晶體的擇優取向度明顯提高,石墨微晶尺寸明顯增大,因此以其為粘結劑制備的石墨塊的熱導率最高。由+32目鱗片石墨和不同量的AR瀝青制備的碳塊樣品在2800℃石墨化后的室溫熱導率和熱擴散率如圖6所示。從圖中可以看出,石墨塊試樣的室溫熱導率和熱擴散率隨著瀝青結合料用量的增加而增加,直到瀝青結合料用量達到14wt%時,超過此用量后試樣的室溫熱導率和熱擴散率略有下降。對于高導熱系數的石墨塊,對導熱系數的貢獻主要來自鱗片石墨(82wt%~96wt%),中間相瀝青和后續熱處理形成的焦炭或石墨起連接和傳導作用。如圖7所示,石墨塊內部有序堆疊的片狀石墨和瀝青粘合劑衍生的石墨顆粒的理想堆疊結構顯示,由于外力和熔融瀝青粘合劑的流動,片狀石墨在模具中優先取向(圖3和4),石墨片堆疊層之間和顆粒之間的間隙被瀝青粘合劑填充和粘合。對于具有相同粒度的片狀石墨,其最緊密堆積排列所需的中間相瀝青粘結劑的量
1)以天然鱗片石墨和中間相瀝青為原料,通過中溫熱壓,然后高溫碳化和石墨化,可以制備出高擇優取向的定向高導熱石墨塊體材料。
2)原材料的組成和比例(鱗片石墨的粒徑/純度、瀝青結合料的種類/性能及其用量/比例)和制備工藝(熱壓條件、熱處理溫度、摻雜處理等。)對所制備的石墨材料的熱導率有顯著影響。以86wt%+32目鱗片石墨和14wt%AR中間相瀝青為原料,在500℃、10 MPa壓力下熱壓成型的炭塊在2800℃石墨化,試樣的綜合熱物理性能(不考慮機械載荷)良好,堆密度大于1.91 g/m3,室溫熱導率高達550 W/(m·k),3000。
3)天然鱗片石墨基石墨塊體材料在生產、加工和成本上具有一定的優勢,其高溫導熱性能優于普通金屬。此外,石墨材料的固有特性有望在一些特殊環境下(如高溫、腐蝕等)取代傳統金屬材料。)用作定向導熱和散熱的熱管理材料。
(充分浸泡和包覆,與其物理性質密切相關)有一個較好的值(如14wt%),低于或高于該值都無法獲得熱導率較高的石墨樣品。粘結劑在高溫下石墨化,形成不同有序度的碳(石墨)顆粒(圖5)。微晶(Lc,La)的尺寸(表3)和微晶沿導熱方向的優選取向(圖7)決定了石墨塊內部導熱通道的完整性和連續性,從而影響石墨塊的整體導熱性[17]。因此,選擇純度高、光學各向異性發達、結構呈流線型、殘炭率高、熔融后粘度低、易流動取向、石墨化后微晶尺寸大、結構更規整的中間相瀝青作為粘結劑,更有利于提高石墨材料的導熱性能。
天然鱗片石墨的純度和粒度石墨塊的高導熱系數主要來源于鱗片石墨,鱗片石墨占成分的絕大部分。因此,鱗片石墨的純度和粒度對其導熱系數有一定的影響。將實驗中使用的天然鱗片石墨原料(純度99.5%)浸泡在氫氟酸中,然后用水洗滌。所制備的石墨塊在室溫下的導熱系數略有增加(~ 10w/(m·k),約2%),這主要是由于去除了一些微量粉塵和礦物質(如二氧化硅、氧化鐵等)。)影響導熱率。但氫氟酸處理對設備要求高,其制備工藝復雜,明顯增加了石墨材料的生產成本。而且鱗片石墨在提純過程中容易破碎,導致石墨塊最終導熱系數提高不大。用不同粒度的鱗片石墨和14wt%AR瀝青粘結劑制備的石墨塊樣品的室溫熱擴散率和熱導率如表4所示。從表中可以看出,石墨塊樣品的室溫熱擴散率和熱導率隨著鱗片石墨粒徑的增大而增大。這是因為鱗片石墨本身具有層狀結構,熱壓時容易沿垂直熱壓方向排列。材料的取向度越高,晶格排列越規則,對導熱越有利,其導熱系數越高。石墨的粒度越大,其本身的缺陷越少,其導熱性和導電性越好,并且具有優選的取向。
熱處理溫度從圖8中可以看出,14wt%AR瀝青制成的炭塊樣品在不同溫度(1000~3000℃)下炭化石墨化后導熱系數明顯提高,這與高溫熱處理過程中中間相瀝青粘結劑的結構演變有關。中間相瀝青是一種容易石墨化的原料,瀝青焦變成炭(石墨)后結構規整,分層堆積取向度為度。同時,在石墨化過程中,隨著瀝青碳-碳網狀平面的生長和發展,產生了或多或少的規則性石墨片層[19],從而顯著提高了其導熱性能。石墨化樣品在300℃時的室溫熱導率高達622 W/(m·k)。
石墨片層的面積比例大,石墨片層之間的界面缺陷少,晶格波在石墨網絡平面內散射的幾率也減弱[5]。因此,由大尺寸鱗片石墨制成的石墨塊具有更高的熱導率。但+20目鱗片石墨制成的石墨塊熱擴散系數和導熱系數異常,因為鱗片石墨太大,無法與瀝青結合料均勻混合,混合過程中容易與陶瓷球碰撞。同時,在熱壓過程中,粒徑過大的鱗片石墨可能因受力不均而變形損壞。另外,粒徑大的天然鱗片石墨比表面積小,達到最緊密堆積的理想狀態所需的瀝青結合料用量可能小于14wt%,更多的瀝青結合料會在塊體中團聚。在后續的高溫熱處理過程中,瀝青會以氣態形式分解揮發,導致材料內部缺陷和孔隙增加,導致石墨塊的熱擴散系數和導熱系數降低。
熱壓溫度和壓力以+32目天然鱗片石墨和14wt%AR瀝青為原料,在不同熱壓溫度(壓力10 MPa)下制備的石墨塊的物理性能列于表5。從表5可以看出,300℃熱壓制備的炭塊在后續的高溫熱處理過程中,由于瀝青結合料的揮發分解,會產生明顯的膨脹,其體積密度較低,石墨塊內部孔隙率和缺陷較高,因此室溫下的熱擴散率和熱導率較低。500℃熱壓制備的石墨塊體積密度高,內部孔隙率和缺陷低,無序堆積石墨的成分也低,因此室溫下的熱擴散率和熱導率大大提高。這可能是由于瀝青在500℃熱壓后,已經完成了半炭化過程,形成半焦或焦炭,在后續的高溫熱處理中基本不再揮發或分解很少[19]。因此,所獲得的石墨塊的體積密度變化很小,并且減少了導致其內部石墨片取向結構無序的因素。當熱壓溫度進一步提高到650℃時,瀝青結合料在壓力下完全碳化,在后續的高溫熱處理過程中對材料內部結構影響不大。因此,石墨塊在室溫下的熱擴散率和熱導率進一步提高,但650℃的高溫熱壓對實驗設備要求更高。
熱壓溫度為500℃,熱壓壓力為4~12 MPa。研究發現,在10 MPa壓力下制備的石墨塊的體積密度(1.91~2.0 g/cm3)較高,其室溫熱導率也較高。材料致密化所需的壓力與模具中的熔融中間相瀝青均勻包覆粘結石墨片所需的驅動力,以及在后續高溫熱處理過程中限制瀝青揮發分解“松弛”和材料體積膨脹的應力有關。所以需要材料致密化所需的壓力。
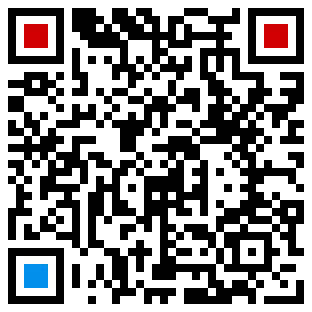
